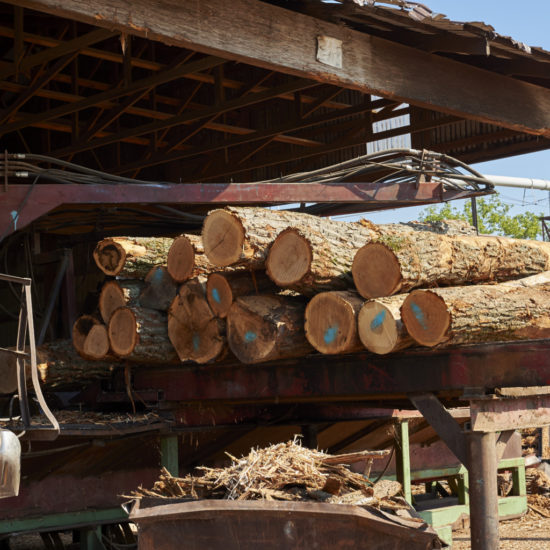
Step 1: Logs arrive at our mill
The trees that go into making our wide plank hardwood floors are hand-selected from local forests in order to ensure the best possible quality and integrity in the floors that we craft. Because these trees grew in the colder region of the northern United States, they produce hardier, more dimensionally stable wood than trees grown elsewhere in the continental U.S.
Step 2: Debark logs
After the logs arrive at the mill, the first step is to debark them using a machine that preserves the integrity of the wood.
Step 3: Mill into planks
The logs are then squared in order to begin forming the planks. We are careful to ensure that our cuts emphasize the natural beauty of the wood. You can read more about the wood grading process here.
Step 4: Cut to length
The planks are then cut down to the proper length, after which they are hand-graded by a wood flooring professional.
Step 5: Kiln-dry
We are dedicated to making sure that you get the highest quality floors possible. To this end, all of the planks are kiln-dried for added stability.
Step 6: Hand-inspect
Each plank is then meticulously hand-inspected by a professional. Any defects are marked to ensure that you receive only the highest-quality planks for your project, and to guarantee that each plank is consistent with its grade.
Step 7: Rip floor board
The planks are then straight-line ripped to create a tighter joint and proper tongue-and-groove alignment. This allows for a stable, more durable floor.
Step 8: Glue and press
We put the same amount of care into creating our engineered floors as we do our unfinished floors. During this step, the boards are prepared for the glue-and-press process. Our mill has truly unique engineered flooring capabilities, so we do everything to ensure that your engineered wide plank floors will be a source of beauty for years to come.
Step 9: Check thickness
Next, the planks go through the thickness planer. This process ensures that the planks are flawlessly consistent.
Step 10: End-match
The boards are then end-matched. We end-match all of our flooring regardless of length or width. The process of end-matching involves trimming each plank as well as milling tongues and groove on the ends of each plank. This reduces installation time and provides a consistent appearance throughout the floor. End-matching also creates a very stable board joint, which helps to ensure the longevity and integrity of the floor.
Step 11: Bundle for shipping
Once the boards have undergone their proper treatments, are the right length and thickness, and our wood floor experts are satisfied with their quality, the planks are bundled to prepare for shipping.
Customization and Craftsmanship
We have extensive capabilities here at our mill when it comes to customization and craftsmanship. We can most likely accommodate your project needs — whether you’re looking for…
A de-nailed, reclaimed wide plank floor for a rustic, artisanal look.
A re-sawed floor for a uniquely traditional appeal.
Or custom finishes and stains right here at the mill for an authentic, hand-finished look.